Continuous Process Optimization of Critical Infrastructure Inspection
speakers
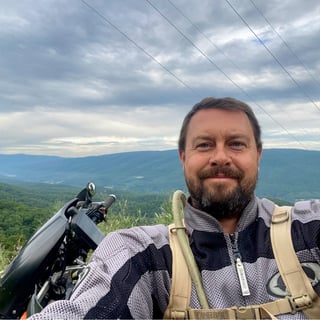
Joshua has 20 years of experience managing a wide range of environmental, exploration, and geotechnical projects and currently is serving as a reality capture technology manager.
Joshua has a diverse knowledge of geo-environmental consulting including site assessment, compliance reporting, regulatory negotiation, feasibility studies, stormwater compliance, soil/groundwater remediation, and aerial data acquisition. Specifically, he has performed soil and groundwater assessments and monitoring, and CAP placement for railroad sites, implemented and operated groundwater remediation systems, planned environmental assessment and remedial efforts providing cost-effective solutions to environmental problems, and achieve regulatory closure. Joshua also has coordinated staff, procured equipment and materials, directed subcontractors, and managed budgets to achieve successful environmental site closures and ultimate client satisfaction. Joshua has experience composing and reviewing technical documents, including work plans, site assessments, remedial action work plans, risk assessments, and final reports for regulatory compliance as well as utilizing unmanned aerial system (UAS) to deliver aerial orthomoasics, digital terrain models, watershed analysis, volumetric calculations, aerial inspection, facade analysis and 3-D models.
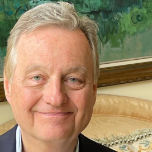
Russ Ellis is a software entrepreneur with 30 years’ experience in building and operating impactful technology companies in the US and UK. In his role with gNext, Russ is focused on delivering the best possible technology and support to the growing infrastructure asset inspection market with the gNext Platform. With the addition of Artificial Intelligence (AI), the opportunity to remove the bottleneck in asset inspection is becoming a reality, and gNext is taking a leadership role in bringing these capabilities to market.
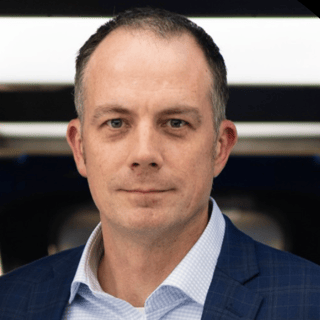
SUMMARY
As critical infrastructure ages, the need for efficient, safe, and cost-effective inspection methods has never been greater. Traditional approaches are often slow, rely on costly resources, and are labor intensive.
Stantec knows this well. That's why they've continued to optimize their drone processes and find new ways to leverage technology to solve complex critical infrastructure problems safely and efficiently.
In this live talk, Joshua Sexton, Reality Capture Technology Manager, shares how Stantec uses Skydio drones to capture data in low-light GPS-denied environments autonomously — processed in gNext to transform the data collected in a challenging environment into actionable insights with a comprehensive operational picture around difficult assets.
Join the discussion to learn:
Innovation Leadership: How Stantec sets new industry benchmarks with advanced drone technology and software solutions. End-to-End Workflow Integration: Combining Skydio's autonomous drones with gNext's software for seamless data capture and processing for digital twins Crucial Capability: ensuring inspections can be conducted whenever required, even in environment drones previously couldn’t access Enhancing Safety and Efficiency: Real-world examples of reducing risks, streamlining operations, and improving project outcomes.
TRANSCRIPT
All right. Well, welcome and thank you for joining us for today's webinar, Continuous Process Optimization of Critical Infrastructure Inspection brought to you by Commercial UAV News and sponsored by Skydio.
I do have a few housekeeping notes to go over before we officially get started. If you need any technical assistance, we first recommend you refreshing your browser. That tends to solve most issues. But if you continue to have any technical issues, please use the Q and A box and I will respond right away.
Note, there is no call in number for today's session. To connect, you just need to have access to either a computer, tablet, or cell phone for audio. And everyone has been muted.
So that you don't miss any shared content or an opportunity to share valuable feedback with us, we do recommend you enabling pop ups within your browser for today's webinar.
For your convenience, everything in the webinar console is fully customizable, so you can move windows around, resize them, and even turn on captions. And at the bottom of the console, you'll find our resources box where you can download the PDF slides for today's webinar. And as always, you can ask questions at any time during the webinar using the Q and A box. And we'll leave time at the end of the webinar to run a Q and A with our speakers. If we're not able to get to all questions, we'll make sure to send those over to the sponsor for follow-up via email.
And finally, this webinar is being recorded and you'll receive a thank you email within two business days with a link to access the on demand version of the webinar. So, look for that in your inbox in the next two business days.
And with that out of the way, I would like to hand the webinar off to our speakers. And, first up is Lee McMillan from Skydio.
Hi. Good morning. Thank you or afternoon depending on where you're at in the country. Thank you for the intro, Laura.
Appreciate that. Once again, I'm Lee McMillan. I'm with Skydio. I'll be more of the monitor moderator of today's webinar.
So we're happy to put up our featured guest. Josh, what do you wanna share right now? Get our slides up and going.
Absolutely.
Alright. So, first off, I'm gonna introduce Russ Ellis who's gonna talk about himself and then we're gonna hand it over to Joshua and hear a little bit about you as well.
Sounds great. Thanks, Lee. I'm Russ Ellis. I'm president of GNEX Labs. We are a six year old technology company and we have our own we have a a platform, cloud based platform for infrastructure inspection, and you'll see some examples of it alongside some great hardware and expertise.
Thanks, Raj. Joshua?
Hello all. Josh Sexton. I'm the Reality Capture Technology Manager here at Stantec, and I also oversee our global UAS program, and I'll go into more detail on that as we proceed along the slide presentation.
Do you want me to take it from here, Lee?
Yeah. Go right ahead. You're up first. Excellent.
Just a little bit of background about Stantec. We're a growing group of employees. We've got about thirty one thousand employees and continuously growing, and we operate over four fifty offices globally. We currently have over one hundred and seventy remote pilots throughout the company, and we have a little bit of a different approach to UAS than many.
We don't consider ourselves a drone service provider even though we have this many pilots. However, we do fly a lot of drones, and I think this photo here is a great example of how we're leveraging UAS at Stantec. This is a bridge engineer, Michael Marshall, and this is just one of the tools in his toolkit, when he's performing a bridge inspection, that he's using as part of the remote sensing tools we have. He's using UAS as a first pass and a way to access areas that are difficult to reach to get visual intelligence and also create three d models determine if they need to do a hands on inspection immediately and also direct those inspections for efficiency.
So that's one of the differences between Stantec.
All our pilots have a day job. They're all engineers, surveyors, geologists, archaeologists, biologists with a passion for getting the best products to our clients, and part of that passion involves them using UAS for both efficiency and deliverables of better work products. And there's a QR code if you're more interested about Stantec. You can find additional information there at that QR code.
So talking about process optimization, I think the first thing we have to do is look at why are we using drones to start with. And traditionally, a lot of our field data collection methods have been very manual, and this image on the left is one of our best pilots in, Florida. This is a biologist, Ray Dennis, and traditionally, he's taken a basin rover out and where he was doing estuary monitoring and redevelopment, he would have to physically march through these marshes and survey those species of interest in with the GPS. That's just very, very difficult, hard work in the southern US where it's very hot. And now we've moved away, from a lot of this boots on the ground survey, if you will, to using a Skydio X ten as his drone of choice. And you can see that it's definitely preferred to have a nice shaded canopy there. He's got a fan in there to keep himself cool and, you know, he's away from the bugs and it just improves the whole user experience.
His quality of life has improved. He's excited about going into the field now, and our data quality has also improved. So I think the first thing about optimizing any program, no matter what hardware or software you're using, is empowering your people and finding the people that are passionate about UAS. Ray is a great example because he is a RC helicopter pilot. He's an FPV pilot. So naturally, it made sense to put a UAS in his hands and get him into our program as a champion for the program to both improve his ability to capture data but also improve the work products that Stantec's arriving.
And as you can see, it lowers our risk too when we are using robotics for data capture versus actually putting people into the field.
As we're digitizing all our assets and we're trying to become as efficient as possible in moving into digital data acquisition, I think it's imprudent to have a go it alone, your philosophy, and that's why we're on this presentation with both Skydio and GeneX.
These are great companies that have listened to us. We've been into the field on numerous occasions with both companies and they listen to us and what we're trying to achieve and help us achieve our goals with their products. A great example are two of our solution engineers and structural engineers meeting together. We have folks from Skydio and Stantec in the photo in the bottom left. This is at the O'Callaghan Tillman Bridge. And having the drone vendor on-site listening to us and help us in helping us achieve our goals was critical on this project.
So it helped our acquisition project. We learned a lot about what the drone could and couldn't do, and they listened to us on what we were asking for to make improvements for the next generation of hardware that Skydio deployed.
So a takeaway from that is this data was collected with the Skydio x two, and you can see the beautiful mesh model on the top right. That was provided by GNXT. This was a collaborative effort between all three companies, Stantec, Skydio, and GNXT, and we were really tickled with the results and the client was so happy that they asked us to repeat this on cadence. So it's a great story to tell here how we all came together in a partnering scenario for a deliverable that exceeded the client's expectations. If you want to know more about that specific effort, there's a QR code in the bottom right, from a LinkedIn Live we did with Skydio kind of as a debrief following that project. But overall, I think it was just a win for everyone. And Russ, did you want to add color to that?
Absolutely. Thanks, Josh. You know, at GeneX, we're we're proud partners with both Stantec and Skydio. With Stantec, we love processing their data, because they consistently capture great data, and with Skydio, we have a cloud to cloud integration and we work very closely with their their field, support folks. They process models on our system regularly and we work together collaboratively to make improvements on both sides, so it's really exciting and the cloud integration makes it even more compelling for our joint customers such as Stantec, so they're able to be able to bring that data over automatically directly from GNEXT.
Thanks for that additional content, and just to add emphasis to this, when we have partners, we can look at the individuals in these photos. Our structural engineers on the ground are fantastic engineers, but they aren't professional drone pilots, but the work product they derive through partnering with our vendors created something that is competitive with anyone in the market, I think. And I think that's the difference. The Skydio hardware and software, the ability to consistently collect great data with that due to the autonomous features in three d scan, and then the easy ingestion into GNEXT are a really winning combination for us.
So the focus of this webinar once again is process optimization for critical infrastructure, and reflecting back on my experience, roughly twenty four years ago back in two thousand, I was collecting, digital field data with an AudioVox Maestro PDA, a CompactFlash GPS, and, ArcPad, and, you know, it was difficult at that time because my background is a geologist, and the peers that I have in the field were still using field notebooks, Bruton compasses, and, colored pencils. And there was a lot of pushback for digital data collection, just like when we moved from using total stations to GPS and the, integration of laser scanners and now drones, there's a constant paradigm shift where, the establishment does push back against new things.
So I think that visualization is now becoming the standard. It's expected on contracts. Everyone in the marketplace is oversaturated with these wonderful, three d models of structures, but we have responsible as to how we're collecting the data. We don't wanna just produce beautiful three d models like you're seeing here, but the data has to be repeatable, durable, defendable, and for a lot of these assets, this is the first baseline data that's holistically viewable for these assets moving forward for the next decades.
So we have to get it right. I think it's extremely important that we talk about that.
And I think data integrity is the foundation of reliable insights and that's something that's not talked about enough in the industry, but we're at a critical threshold where we are beginning to move from static deliverables, which had been traditionally line work and PDF documents and a couple of photos to holistic three d models. And as we collect data over time and cadence data for change detection, all this data has to line up consistently and we have to be able to defend it. So it's truly important that we go into data collection with a plan for our acquisition and that we're looking at fit for purpose data for our deliverables from the start.
So one of the most important things we can talk about is geospatial control. We've got some ground control point examples here and on every asset that we're collecting data on that we're gonna take a measurement on, we need to see those ground control points. And it really doesn't matter how we're pasting those points. It can be a printed target that's autonomously recognized by the software.
It can be a purchase target like in the top right in an aerial instance where we're doing nadir mapping, or we can even print those targets ourselves with a three d printer.
But we need to establish control with high accuracy GPSs or with total stations or laser scanners to make sure that our cadence data is gonna hang consistently over time in real world coordinate systems. So it's usable beyond our initial collection, but what virtual twins are designed for, cadence survey over time, we can understand how these assets are changing.
And, Josh, I'll I'll, add in here that I'm not even going to begin to change or try to change your mind because I'm in I'm in total agreement with you on that.
At GNEX, we support, ground control and highly encourage it.
And I would also say that we've seen some very interesting quote ground control points being used even, you know, things like storm drains, and things of that nature that you really have to try to figure out. But at any rate, it's effective, it's efficient, and, it adds so much more accuracy to any survey or inspection.
Back to you, Josh.
Yeah. I agree a hundred percent, and we're talking specifically about photogrammetry here within the Skydio and GeneX platform, and I think that's a key issue with photogrammetry is we need to see good ground control because even if the work product is accurate that we're deriving from the photogrammetry, we have to be able to defend that. And without the ground control, it's almost impossible to defend any work product.
But the great thing about this is both GPSs are becoming, cheaper to procure, more accurate, with more course networks throughout the world and then also the hardware that we're collecting data with is becoming much easier to use and that's one thing that we wanna highlight here with our relationship with Skydio and also give them credit for what I'm gonna call is democratizing data acquisition.
We can see in the top right hand corner, that a contractor had performed some drone surveys before on this asset. This wasn't us, but we did detect this drone when we were creating a three d model. And with GNXT, it's kinda cool because we can see the three d mesh model on the left and then zoom in on the raw image on the right.
And it's also interesting because when you've got a Sprat team, the first thing those guys wanted to do is run down and figure out whose drone it was. So we did clean up the trash here that we detected, you know, but no matter what you're doing, there there's gonna be incidences. But, the fact that Skydio makes data acquisition so much easier. Clicking on this video here, we can see an autonomous Skydio x two on the O'Callaghan Tillman Bridge.
The drone is collecting the data autonomously. We've set the boundaries that we want it to survey, the GSD and the front and side overlap, and you can see what the scan looks like on the controller.
And this is critical for our inspection teams because they can focus on the operational environment and the surroundings that the drone's operating in. It increases their confidence because they are aware that the drone can sense and avoid objects in that environment, and it creates consistent data acquisition because we know the front and side overlap and the GSD is gonna remain constant throughout the inspection.
So these are some great things that developments with both hardware and software and then integration into, solutions like GeneX are allowing us to rapidly both collect data for visual intelligence, but then make that data actionable when we need to measure features and defects, especially when we start applying, machine learning analytics as we'll discuss a little later.
Yeah, Josh, this is Lee. No, thanks for that. And yeah, we'd like to say at Skydio, one of the things we like to say is our drones are, easy to fly, hard to crash. And we do that through, an autonomy system that's built in. Each Skydio drone has six navigation cameras that build a three hundred and sixty degree picture of the world.
So what we try to make that, I'll take away the technical stuff, but we try to do is just make it so the pilot can focus on that data collection piece rather than, the position of its drone. Because the drone's gonna avoid those obstacles and then get the shot you need. And part of that, navigation camera thing, system as well, allows you to fly in areas where other drones can't. So you guys can get really close under those decks, you can fly where GPS connectivity is poor.
So it allows your folks to get underneath those decks in the tight spaces where some other drones don't. So, it's gonna tee up some stuff I'll probably talk about here in a few minutes, but I just wanted to point out the autonomy piece there. Thank you.
Yeah. That's a great point, and it allows our teams to be more confident, with that data collection, especially when we're flying in high casualty environments like up between the girders of a bridge. And once again, we're deploying structural engineers and biologists and archaeologists that are flying in these high casualty environments and their day job isn't a professional drone pilot, but giving them a piece of hardware with smart software behind it where it can safely navigate those environments and they can collect that visual intelligence is great. And we can also put these drones into environments that may be hazardous, both for our occupants just as first visual intelligence, and we're gonna talk about that a little more later, but being able to collect data and not have to shut down roads with snooper trucks and causing congestion, having individuals climbing bridges, which do create a lot of interaction with the general public.
They're interested in what's going on. Maybe they'll lose their attention span. So, yeah, this is a great thing that we're implementing robotics for data acquisition and it's improving our efficiency and the safety of everything we do.
Thanks. Hey, before we move on, I just want to jump in here. I got a question. I know we're gonna save some questions to the end.
So this is another reminder, start pouring in some questions if you have them. But I did have one from Sasha who who asked a question about our, obstacle avoidance and she says, could drones reliably, detect conduits and cables to avoid collisions? And the answer there is yes. With the X ten, we are I don't have the exact, measurement off hand, but we can definitely see wires, small things like conduit get up in between those girders and you can fly that pretty confidently.
The system has multiple layers of obstacle avoidance that allows you to kind of pick a setting that's right for you.
It'll normally build a pretty wide bubble around it, but you can move it into a close obstacle avoidance if you need to get a really close shot up to maybe like a foot away. So it's pretty reliable and with the X ten and its amazing processing power we have on board, it's seen smaller and smaller objects all the time to avoid.
Thank you.
Yeah. And to add to that, Lee, our rule of thumb is the object needs to be at least a half inch or greater. I'm sure that the drone can detect those objects, but that's our general cutoff. If the limbs of a tree, for instance, or wires dangling from a structure are less than a half an inch, we try to avoid that area and fly it manually.
But jumping into some x ten data, like you discussed, kinda queuing up this video, this is a small rail bridge, that we collected with the Skydio x ten l, and this effort took about an hour. Ninety five percent of this collection was autonomous. I collected a little bit of data manually, just on the underside of the steel elements there just to make sure we had enough capture, but it probably wasn't required.
The great thing about this effort here is this was a very complex acquisition. There's lots of overhanging vegetation that's been clipped out and it's in a deeply dissected valley that this stream was running through that this overpass went over. And the lighting wasn't great, so the ability for the drone to collect very visually pleasing photographic data, autonomously and completely automatically without changing any camera settings and then adjust that into a visual intelligence platform like GeneX was a real win here. So I'm gonna click the video here just to run through and we can see how sharp this steel came out and we can see that the the model's really visually pleasing, but there's no gaping holes in it either.
The air triangulation stitched really well together, all the photos pulled in nicely, and we've got really high accuracy, rich measured texture here, on this model. And the ability to walk a client through a model and we can toggle on all the defects here and show them within context, not a written report or a photograph, but actually walk them through the model. We can show them where fasteners are standing proud, where there's ballast that's getting ready to drop into the roadway, where we've got rusting. It's a real differentiator for our clients because they can see the actual extent of the structure without visiting the site.
And once again, it allows us to show our teams and collaborate with them and then take this model and use it as the basis for future design and upfits, when we see problems and we need to make changes.
Russ, did you want to speak to this acquisition any?
I would love to. You know, the model came out well because it was well collected data with a really great sensor. And when those things combine, then the models can come out like you're seeing right now. And we're really pleased with the results of it as I know you are, Josh.
And we're looking at a structure that that, as you said, is very difficult to be able to collect efficiently or effectively.
But, you know, with the proper tools, it can really work.
And with the GNEXT platform, the tools that we try to focus on are the tools that are most necessary for the field, and while we see a lot of annotations and measurements on here, these were actually done manually, and the next video will demonstrate, some of our AI capabilities, and and be able to discuss the difference between those two. But my hats off to you on on the data capture, and I'd also say I'm sure glad that is a disused, real LAN right now.
Thanks, Russ, for that, and, you know, and that's once again we're talking about fit for purpose data. This was just a quick model to prepare our teams for an actual inspection and walk through some issues with our client. The next model that we're going to be illustrating is a little more in-depth. This was collected with the Skydio X two, and for level of effort here, this model did take about a day to collect.
We never flew over live traffic. There were some delays in the collection because we had to set up traffic control below the bridge, so we were never flying over live traffic and could see the underside of the deck. The top side of the deck that was collected was all collected obliquely, which wasn't ideal, but we were able to get good visual information off that deck and we had enough control to use it for our purposes. And we ran AI defect detection on this along with AI two d, cross sections.
And it's just a great showcase of how useful this platform is. We can see some of that great data collected with the X two, really high resolution raw photos, and that merged into a beautiful model. We've also got some video here, the LRV video that we can tag in there if we need. And throughout this model, you'll see a ton of ground control placed all over the structure that was shot in by a PLS in Maryland that's on staff with us.
So it's a very well controlled, submillimeter GSD model, and now we're kicking on some of those AI defect layers. This two d plan view was automatically generated with machine learning on the GeneX platform, and these, features that are vectorized were also autonomously generated. And we can see here that we've got a patch, but we've also got cracks propagating through that patch. So this is telltale science on the fact that that patch wasn't installed correctly.
And having the ability to quickly get to a ninety five percent work product, we're still always gonna go through and check the vectorization for accuracy. But being able to distill all the information we're capturing and get it into an exportable CSV or a DXF file or a textured mesh model and then being able to use it in a work product and show heat maps of where we have areas and total volumes of repairs. It's a wonderful tool to have, to be able to take data from photography and generate a product like this.
And, Russ, do you want Josh, I would add that with our AI, GNEXT Inspect Assist, we are really experiencing phenomenal results and our customers are as well.
As we're looking at this bridge deck, twelve megapixels never looked so good, right?
This was, you know, well captured data, so we're able to model it effectively. And as we get to the AI was only run on the bridge deck, so as we get back to the bridge deck, we'll be able to see is just as you pointed out, the effects of of that, are really, game changing. You know, drones drone capture data merely pushed the bottleneck down the line, and, you know, it it didn't remove it because the inspector still had to sit and visually look at it and make all the annotations and make all the measurements and create the reports.
With AI now, it's a validation process, so if we get up back up to the bridge deck, just a little further along.
I was just going to highlight the fact that, you know, we were able to collect all this data with very limited impact to traffic. We were only closing one lane underneath the bridge on a sparsely used surface street, and the drone was able to get up in these girders and around, this wiring, with no issues. So that was a definite win to the question earlier, can we operate, you know, around, wires and vegetation? And, definitely, the drone was able to safely navigate those areas. Let me get to that bridge deck for you again, Russ.
Perfect.
So being able to get underneath the bridge like this and capture that data, yep, that it's a game changer for bridge inspection without a doubt. And, you know, autonomous flight and collision avoidance makes all the difference. Now we're getting to the bridge deck, and we'll see, we're almost there. We'll see the the results of it.
You know, the video capability is significant. The Skydio drones collect video and and LRV format, and we highly recommend to our customers to upload that because it creates a whole new vivid, amount of texture, and understanding to it. We're looking at an actual, image now, but the video when they click on that, now we've got video running, you can pause and annotate anywhere, you can download any images that you want and all annotations are swept up into the reporting so you can, you can it just creates seamless reports.
Yeah. Sorry about the delay here, everyone. The bandwidth of of sharing, through the teams.
You know we're right. So here we are with our our AI Inspect Assist, and with GeneX we not only annotate, but we quantify each individual defect and it's got its own unique ID. So if you the next time you capture and run AI, we can show change on a specific defect by defect basis. And as Josh pointed out, you know, understanding where former patches were made and remediations were made and where they're failing now really helps you understand how that asset is performing over time, which is a game changer. You were seeing hovering it over any of those those defects, you get all the specifics about it, which really provides, you know, significant this this is what is changing and taking the bottleneck out of inspecting, and allowing it to be just validation at this point.
Thank you.
Excellent. And and to this point, beyond the great AI defect detection that GNXT is offering, you know, lots of folks are creating highly accurate three d models, you know, to this quality or even better. You know, our data is fit for purpose, specifically for client needs, no more, no less. But, you know, creating beautiful models isn't exclusive to either hardware or software, but I think the things that are really changing is the ability to extend the usefulness of the hardware we've been talking about into new environments and that comes with Night Sense. So I'm gonna turn this over to, Lee to discuss Skydio's Night Sense.
Yeah. Thank you very much.
Yes, Skydio Night Sense, the fun improvement. As kind of Joshua was outlining at the beginning of this is we go on-site with customers a lot and we learn a lot. One of the things that we wanted to bring with the X ten was the ability to have it be modular and add on and make it better over time. One of those modularity pieces that we brought to the table is a module we called NightSense and comes in two forms, it's either an IR light so you can kinda operate in pretty much darkness at night or a illuminated light, which is probably the better fit for the inspections that we'll talk about here.
But what that uses is those same navigation cameras that are on the drone are still used. We put an attachment on both the top and bottom of the drone and then it illuminates the area. So, and that illumination is bright, have our visible night sense on. And what that allows you to do is kind of as this gift showing is that's a park at night and we can safely navigate around trees, objects, the same as we could during daylight.
So it gives you that confidence, that that same confidence to fly at night as you could in the daytime. And if you switch slides here, what that kind of unlocks on the inspection side is you take the ability with the Night Sense module to see in the dark, you couple that with being able to operate in GPS to night environments, and now you can truly do inspections in, environments that have no GPS connection at night or in low light. So, you know, if you've got a bridge that's just really like wide and creates dark areas, even the daytime, it could be tough to get some images. Night Sense can help unlock those.
The drone has placements for a spotlight and one of our sensors on it actually has illuminated light as well. So we want to bring light to the images you're capturing. And then what that allows you to do is kind of autonomously, capture those images in a nighttime environment. And I think that's gonna tee up the next model.
So I'll hand it back to Joshua.
Thanks, Lee. And this is one of the most exciting additions to the Skydio X ten line for me personally. And there's a lot of reasons for that. The ability to take hardware that we've standardized on for data collection that our staff are both familiar and confident with and that are using on a daily extend its utilization into areas that were never capable of being assessed without a specialty drone before.
And there's nothing against the fantastic confined space specialty drones that are out there. But if you already have a tool in your toolkit that you're familiar with that is easy to fly and being able to extend that into environments like we're seeing here, that really changes the paradigm of how you're gonna use that technology, where you're gonna use it, and the ability to have it ready when you need it, at quick deployment. It's not a single drone that maybe the what only a few people within the company know how to operate or that resides in a specific location, but, you know, the majority of our staff are confident operating Skydio drones.
They're familiar with them, and now we can put them into, environments like you're seeing. So the one great, benefit of my role is that I get to test everything to the ragged edge of failure before everyone else so I can set the guidance moving forward for our whole program of what it can do and what we probably shouldn't. And with SkydioCare, for better or worse, I know that Skydio is going to stand behind their product if I do something silly and they're still going to honor their care. So I do appreciate that within a company that they are that confident in their solution that they stand behind it if there is an incident, which, you know, there are very few.
But as an example, the day we got our Night Sense, the first thing I did was place the payload on the drone and took it into one of our storage rooms with no windows and tried to crash it because if anyone crashes the drone, I wanna be the guy that gets yelled at. So, you know, I flew it around all the storage we had in there, shelving and so forth, and it operated wonderfully. So I left the office. I went home where there's a box culvert at my farm and I flew it through this box culvert that you see here.
And once again, the drone operated superbly. It went in and out of Night Sense as needed. You can see some vines hanging down there in the box culvert. I didn't ask the drone to avoid those fines, and I didn't use three d scan.
This was all a manual test of the drone, but just learning the limits of the hardware and the software behind it, where it operated and performed within the best of its capabilities, and once again, it worked great. So at that point, I was pretty confident. I called a friend of mine and he has a tunnel going to his home. So I said, hey, can I fly your tunnel tonight with a drone?
And that was an interesting conversation. He was like, well, go knock yourself out, but, the caveat is I'm not home, my gate's locked, but you can you can climb over the gate and and do what you need to do. So this offers a unique kind of idea of what this drone's capable of. We were able to take, with no ancillary lighting, without actually physically accessing our area of interest in the dark in the GPS denied environment, collect data on an asset, and this was so well integrated that we were able to do it the day we got the solution.
Now we were familiar with the hardware, but the Night Sense payload itself was new to us, but it was easy to ingest and figure out.
So within twenty four hours, we turned a drone that would fly well in the day to a drone that would fly well at day and night. And going through what that model looked like, three d scan isn't currently enabled, so the model that you're looking at here was captured manually, but it was captured at ten thirty at night in complete darkness with no ancillary lighting from a distance where you could see that the ground control station was sitting on a tripod, and the model came out very good. We've learned a lot since this initial test.
You know, we've learned a lot of camera settings that improve the quality, but overall, I was delighted with the ability to capture both video and photogrammetry data and then stitch it together in GNXT. And, you know, having a partner like GNXT, I called them and I said, hey, I'm trying to figure out how to model tunnels. I've got an example. I think it'll work.
I've processed it in a couple other solutions, but I would like to see what it looks like in GeneXt. And it was by far the best when we did process it in GeneX, and I was just delighted with the quality of the model that was produced. In the top right hand corner is actually a point cloud from that model shown in Cloud Compare, and you can just see the rich color and density of that point cloud from the processed photogrammetry data, and then in the right hand side, you can see the three d model and a zoomed in image of the raw data that was used to stitch that model together, and and this is useful enough for a lot of inspection capabilities and allows this drone a completely new avenue across all our verticals to go into tunnels, dam galleries, mining portals, warehouses, crawl spaces, places that maybe we need to create a model or we just need visual intelligence before we put one of our staff members in that environment, and that's one of the most exciting things about the Skydio solution with the X10 to me to extend that capability across all our pilots and let them be able to collect data at this high level in these challenging environments.
Russ, did you want to add color to this?
Absolutely. Thanks, Josh. You know, for an out of the box experience, meaning you you you just strapped it on and took it out and and and captured this at night, it came out so well. And I I can also confirm that that your modifications and the the some of the setting changes that you've made are a big improvement, but I'll tell you what, this was this was a great out of the box, kind of an experience. And I would agree, now we're moving into very challenging environments, and it just opens up more and more critical infrastructure assets to be inspected, properly utilizing drones with the, you know, with like the Skydio with with light kit. Thank you.
Excellent. And if you're interested in seeing that model, there is a link to the video at that QR code.
And, you know, ever since we got the Night Sense, we've been deploying it to all our different verticals.
They've been throwing it on their X10s, testing it in tunnels, in dam galleries, and we're collecting a lot of data that's really, really changing our inspection efforts in these challenging environments.
So I'll kick it back to you, Lee.
Cool. Well, Josh, I appreciate on that last one, we appreciate the torture test you gave it on day one. So good to see everything, worked well and we got that awesome model. That was fun to see.
So let's see, let's get into the questions. Once again, reminder, throw those questions in the q and a box and we'll we'll get to them. I did have a couple flow in. First one here is from Robert, who I think must have an X10 because his question is, is the NightSense payload the same IP rating as the ten? The answer there is yes. So it's the same IP fifty five rating as the x ten and that means you can operate in kind of light rains and snowy conditions as well.
I do not know how that will impact your inspections if it's getting rained on, but my my guess is your your video quality could be a little inhibited by the rain, but you're gonna have the same flight characteristics there.
Alright.
For my next question from Devin here, how does Stantec ensure that the data captured by the drone is accurate and actionable?
Do you have any other examples that you wanna give?
So where we have to take a measurement, we'll always engage a professional licensed surveyor, to set ground control, and then with the photogrammetry report, we'll have that surveyor review the RMS error of both our control points and the checkpoints that we place over the structure, and we'll get that verification third party, even if it's internal, through a surveyor because we do want to make sure that our data is defendable, and that's a pretty standard workflow.
Okay. Perfect. And then I got another question here, from Tyler. Tyler asks, what's the maximum distance that NightSense can detect a large obstacle? I guess that one's for me, so I'll take it.
The answer there is we try to use the same optical avoidance capabilities that we use day or night. So the modules you put on illuminate the area that the drone would need to see those obstacles. So you're gonna get the same type of characteristics.
Generally speaking, I tend to When I play with it, you know, around my house and try to crash it myself, you kinda see a bubble build around the drone that's, probably a little over three feet on a normal obstacle detection. And then you can turn that down as I said, you know, wouldn't recommend doing that in windy times, but, you do have the optionality to kind of reduce that sphere of obstacle avoidance there.
Alright.
Let's see here. Got some more questions flowing in.
Got another one from Aaron here. What are some of the key skills or training requirements from operators using autonomous drones, especially in those GPS denied environments? I'm not sure that's probably yours.
Sure. At Stantec, we have a pretty regimented program. We require all our pilots to hold a regional certificate. Here in North America, the big ones are the FAA one zero seven or Transport Canada Basic and Advanced, and all the regions we operate, all our pilots are required to have a certification, allowing them to operate in that nation's airspace. Additionally, we have an internal vetting program. We want folks to build confidence, with that crawl, walk, run mentality, so we have a mentor program where we'll mentor pilots through a basic operator certification that's internal to us and then move them to an advanced certification.
You know, the great thing about the Skydio solution is, and especially when you're in GPS environments and interior spaces, you're not operating in the national airspace.
So, you know, there's not a concern of conflict. With a great drone like Skydio, it's gonna have collision avoidance. So there isn't a lot more skill required, if you're only collecting video, data of that asset. Now if you're doing photogrammetry, that does require more skill, especially if you're doing it manually where three d scan isn't enabled, with Night Sense currently. So, you know, that takes a little more practice. But we try to train people, for the data they need to collect for their work products.
Alright. Very good.
Next question here from Zechariah. Do you use RTK?
I'm gonna take this one. The x ten, I'm talking about the modularity of it. We are building a RTK module for the x ten. It's available for purchase today.
Right now we're working on some of the final testing for that and we'll hopefully be rolling it out, later in the year. So yes, we'll have RTK and also that'll be worked, in conjunction with PPK stations as well. So good one there.
And then I'm gonna actually this is from Joseph.
I'm just gonna throw this one to you, Joshua. Joshua, it says, how far away can the thermal camera be used before image quality degrades? So Joshua, do you you all use any thermal in your, models? And if so, do you have any, like, recommendations there?
So we do. And it's primarily for, anomaly detection. So if we're looking at seepage through a dam or a headwall, for instance, if we're looking for wildlife detection, and and that basically comes down to GSD. How big of an area are you looking at?
You know, are you looking for a field mouse, or are you looking for a thirty meter karst conduit? So it really depends on what you're trying to capture, but you have to plan your acquisition appropriately. So figure the GSD that you need to see your object of interest specifically, and then target your offset from that, whether it's lateral or if you're doing a nadir mission, a two d mapping mission vertically, so that you can achieve success.
Alright. Thank you for that one.
Let's see here. I got one from Mike. Russ, this is probably for you. It says, can you explain how the integration between the Skydio DREMS and GeneX works?
Absolutely. And, you know, while while GeneX is is drone and sensor agnostic, we we certainly we we love working with Skydio, and we've we've created a cloud to cloud integration.
So it just makes it really simple once you bring your drone in from the field when it connects up to to Wi Fi, the data is automatically uploaded. You can go and create a project in Gnext and and just point back to the the Skydio cloud, and select the the dataset that you prefer, and it just goes over seamlessly cloud to cloud. So, yep, absolutely. It, works well, and and, and it seems to be a growing favorite.
Alright.
Got another one here from, let's see, Margaret, who asked, do you have online training for pilots about the drones? So and this is, I guess, one for Skydio here. I'll take that. Yeah.
We do have, some online training in Skydio Academy. We walk you through how to use and fly your drones. We also have some partnerships that if you're kind of growing a drone program, we can connect you with some folks that will help you obtain part one zero seven licenses. So yes, we'll train you on your old tools on our tools, and then we'll help you get the licenses you need to operate there.
Let's see. I got a couple more questions still flowing in. Good to see an active audience here.
Let's see this.
Oh, this is probably a question for you, Joshua. It's on one of the models you showed. I think it was it says, did you add manual photos when doing some of the three d models or is it a hundred percent from our three d capture?
So a lot of times we have to do a mix of both. Three d scan does a very good job consistently of capturing an asset, but a lot of times we cannot use three d scan exclusively because we can't fly over live traffic. For example, on the, transportation bridge, the highway bridge that we saw, the deck was collected obliquely. We stopped one lane of traffic.
We would fly obliquely on, both sides of the bridge, then move over to the other side and fly obliquely. So a lot of times, it's a mix of the two. We'll use three d scan where we can let the drone rove where it will, and then we set boundaries so we have limits there and a geofence so we won't have interactions with pedestrians, for instance, live traffic, train traffic, and what have you. It's also always good to collect additional cadence photos of your asset.
We like to collect obliques away from the asset and collect additional photographs underneath the asset, specifically in challenging environments, and at those points in time, we may actually adjust some of the camera settings to make sure that we have proper exposure. But overall, if the asset doesn't have any conflicts, there's no vegetation that we're concerned about hitting that's really fine or blowing in the breeze, we let three d scan, collect the majority of the data.
Great. And Lee, if I could just add I'm sorry. If I could just add one thing. And with GNAX, we we we also support, handheld or or or inspection images to be uploaded and be reviewed as part of that inspection process in addition to to vehicle collected data and, three sixty images and video. So sometimes you've got to use different types and, we we GeneX supports that as well. Thank you.
Alright, I think I have time for about two more questions here and that's kind of coming to the end of our list here.
I'm just gonna throw this one out here. I may answer part of it, but then both of y'all feel free to chime in. It says, what program or what's the drone equipped with to store the data it's using and what methods are used for sharing? I'll take kind of the first part of this. The x ten does have SD cards that collect all the data and there's a couple ways you can get that off. You can either pull the card out of the drone and just manually do it or you can connect it to a WiFi system and automatically upload it, to the Skydio cloud, which would give you that cloud to cloud connection that Russ was talking about.
Joshua, Russ, you have any other recommendations for folks on pulling data off or best best data use practices?
So, for Stantec personally, when we're collecting data, in between every capture, especially if we have questions, we'll pull the data off and switch SD cards and we'll have one staff member, if we have them available, start reviewing the data to make sure that we don't have any image blur. There was a comment about dust, exposure, and we'll start checking that data while the pilot is actually flying the next mission, and we'll also go ahead and back up that data because, you know, we always have the possibility of something happening, when we're collecting data. And as soon as we're done with, one Element capture, we'll pull that data off, back it up, and start reviewing it, put in another card, and, send the drone back to work while we're, reviewing that data and backing it up. As far as getting it to cloud solutions like GNEXT, generally, that's a a web push through a browser.
Perfect.
Alright. I got one more here, I think Josh is probably for you. It says, have you quantified the efficiency improvements from using drones over some of the more traditional methods and any metrics you can share for that?
So it it's really hard to quantify all the value that robotics brings, when you factor in the fact that we're improving, the worker experience and data collection in so many cases. We're taking folks out of bucket trucks, off rope. We're lowering congestion congestion to the general public, so we're being better stewards of the work that we're performing. But technically looking at it, you know, we're saving a tremendous amount of time with data acquisition and three d modeling in most cases, and it all depends on if we're collecting video for an inspection or we're physically creating a three d model that we're reviewing.
But being able to autonomously do defect detection if we have to vectorize defects where we may have hundreds of thousands of crack and spall and vegetation and rust and paint peeling and all the defects that GeneX has, being able to get to a ninety five percent work product, you know, it's several orders of magnitude quicker to use machine learning through a platform like GeneX than to manually ask our staff to vectorize those features, you know, on that workstation.
Great to hear. Russ, do you have anything to add there?
Yeah. I would just say that to my to a point I made earlier, AI is that game changer that takes that bottleneck out of the process, and out of the way. So now an inspector can be validating data instead of trying to find all the the defects and measure them and and do that all manually. So that's a that's a big differentiator, and I think that what we're seeing now is the gates are open, for just incredible results. And I have had we have had a customer tell us on a very complex, hydro project that they were able to save ninety percent of their time for inspection and for report generation by utilizing G next and with our inspect assist.
Alright, good to hear. Well with that, want to hand it back to Lauren. I'm pretty sure if I think I got to most of the questions, but if there's any that we missed in this queue, I will definitely hand those off to our team and we can get back to you on that. So Laura, over to yours.
Great. Thank you so much, Lee, Josh and Russ for a great webinar today. I do have a few housekeeping notes to go over before we officially close out.
As a reminder, you'll receive a thank you email in the next two business days that will include a link to access the on demand version of today's webinar, as well as the slides. So, for that in your inbox in the next two business days. Also, if you could please fill out the short evaluation form that This will help us better serve your needs in future webinars, and your feedback is greatly appreciated. Thank you again to Josh, Russ, and Leigh for a great webinar today. And thank you to all of our attendees for taking the time out of your busy day to join us. This webinar was brought to you by Commercial UAV News and sponsored by Skydio. Thank you all and have a great rest of your day.
Thanks, everyone.
Thank you. Take care.